1.Triple-Function Efficiency for Modern Production Lines
Our integrated filling, capping and labeling machine combines three critical packaging processes into one high-speed automated system, delivering unmatched efficiency for:
-
Food & Beverage
-
Cosmetics & Personal Care
-
Pharmaceutical & Healthcare
-
Chemical & Household Products
2.Complete Packaging System Components
1. Precision Filling Module
-
±0.5% volume accuracy for liquids/pastes
-
Adjustable from 10ml-1000ml
-
Clean-in-Place (CIP) capability
2. Automatic Capping System
-
Torque-controlled tightening (3-25Nm)
-
Handles screw caps, snap lids, and press-on caps
-
98% seal integrity rate
3. High-Speed Labeling Unit
-
±0.3mm placement accuracy
-
360° wrap-around or front/back labeling
-
Vision verification optional
4. Intelligent Conveying System
-
Variable speed control (5-30m/min)
-
Anti-slip bottle handling
-
Quick-change guides
5 Key Efficiency Boosters
① 80% Labor Reduction
-
One operator manages entire packaging process
-
Eliminates 3 separate workstations
② 3× Faster Throughput
-
Processes 120+ bottles/minute
-
Continuous motion technology
③ 99% Consistency Rate
-
Servo-controlled precision
-
Automatic rejection of defective units
④ Easy Changeovers
-
Recipe storage for 50+ products
-
Tool-free adjustments (<5 minutes)
⑤ Unlimited Adaptability
-
Handles containers from 50ml-5L
-
Compatible with glass/plastic/metal
Technical Specifications
-
Power: 5.5kW/380V/50Hz
-
Footprint: 3.2×1.5m
-
Materials: 304 stainless steel contact parts
-
Certifications: CE, GMP, FDA-compliant models
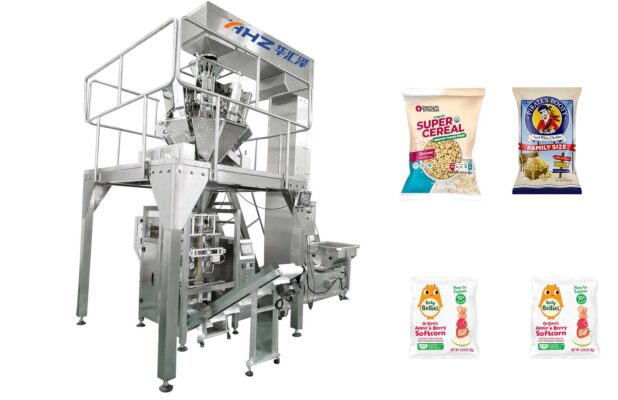
3. How Does a Filling, Capping, and Labeling Machine Work?
A filling, capping, and labeling machine typically consists of three main stations, each performing a crucial function:
3.1 Filling Station
The first part of the process is the filling station, where containers (typically bottles or jars) are automatically filled with the product. This could range from liquids (like juices or oils) to powders (such as spices or protein powder). The filling station ensures that each container gets an accurate and consistent amount of product, eliminating the risks of overfilling or under filling that might occur with manual labor.
Operators can select different filling mechanisms based on product characteristics:
-
Volumetric filling: Common for liquids and semi-liquids, this method fills containers with a set volume of the product.
-
Gravimetric filling: Used for powders, where containers are filled according to weight.
-
Piston or pump filling: Suitable for products with varying viscosity, such as sauces or creams.
3.2 Capping Station
Once the container is filled, it moves to the capping station. At this stage, the machine places caps onto the filled containers and seals them tightly. Capping can involve a variety of systems, such as screw caps, snap-on caps, or press-on lids, depending on the product and the type of container. The capping process is crucial for preventing leakage, contamination, or spoilage of the product inside.
3.3 Labeling Station
The final step in the process is labeling. After the containers are capped, they are moved to the labeling station, where labels are automatically applied to each container. Labels can include important information such as the product name, ingredients, brand logo, expiry date, and any relevant warnings or instructions. Modern filling packing machines, capping packing machines, and labeling packing machines can apply labels precisely and at high speeds, ensuring that each product looks professional and is compliant with industry regulations.
4. Benefits of Using a Filling, Capping, and Labeling Machine
The integration of a filling, capping, and labeling machine into your production line can significantly improve several aspects of your business:
4.1 Increased Efficiency
By automating the packaging process, these machines can greatly speed up production times. Unlike manual labor, which is prone to fatigue and errors, automated systems work continuously, reducing downtime and increasing throughput.
4.2 Enhanced Consistency and Accuracy
One of the biggest advantages of these machines is their ability to consistently fill, cap, and label products with high precision. This consistency reduces errors that can result from human mistakes, ensuring that each product meets quality standards.
4.3 Cost-Effective Production
Automating your packaging line reduces the need for manual labor, saving on wages and associated labor costs. Additionally, fewer errors mean less waste and rework, further reducing operational costs.
4.4 Improved Hygiene and Safety
Manufacturers can design automated filling packing machines, capping packing machines, and labeling machines to comply with stringent hygiene and safety standards.
For industries such as food and pharmaceuticals, ensuring that products are sealed and labeled in a clean environment is crucial to preventing contamination and complying with regulations.
In short, filling machine , capping and labeling machines are an ideal choice for improving production efficiency, reducing production costs and ensuring product quality. With the continuous development of automation technology, filling, capping and labeling machines will play an important role in more fields and promote industrial production towards intelligence and efficiency.
Why Choose Our Integrated System?
40% smaller footprint than separate machines
30% energy savings with smart power management
24/7 technical support with spare parts guarantee
Upgrade your production line today! Contact us for a free efficiency analysis.