Application
Vertical packaging machine is an efficient, intelligent and safe modern packaging equipment, which is used to automatically put products (such as Vertical packaging machine for liquids, Vertical packaging machine for powders,Vertical packaging machine for granules, etc.) into bags and seal them.
Many different industries depend on this, mainly including:
- food industry
- pharmaceutical industry
- daily chemical products industry
- household products industry,
- hardware industry, chemical industry, and furniture
- lighting and other industries for bagged products filling
- sealing, coding and other processes.
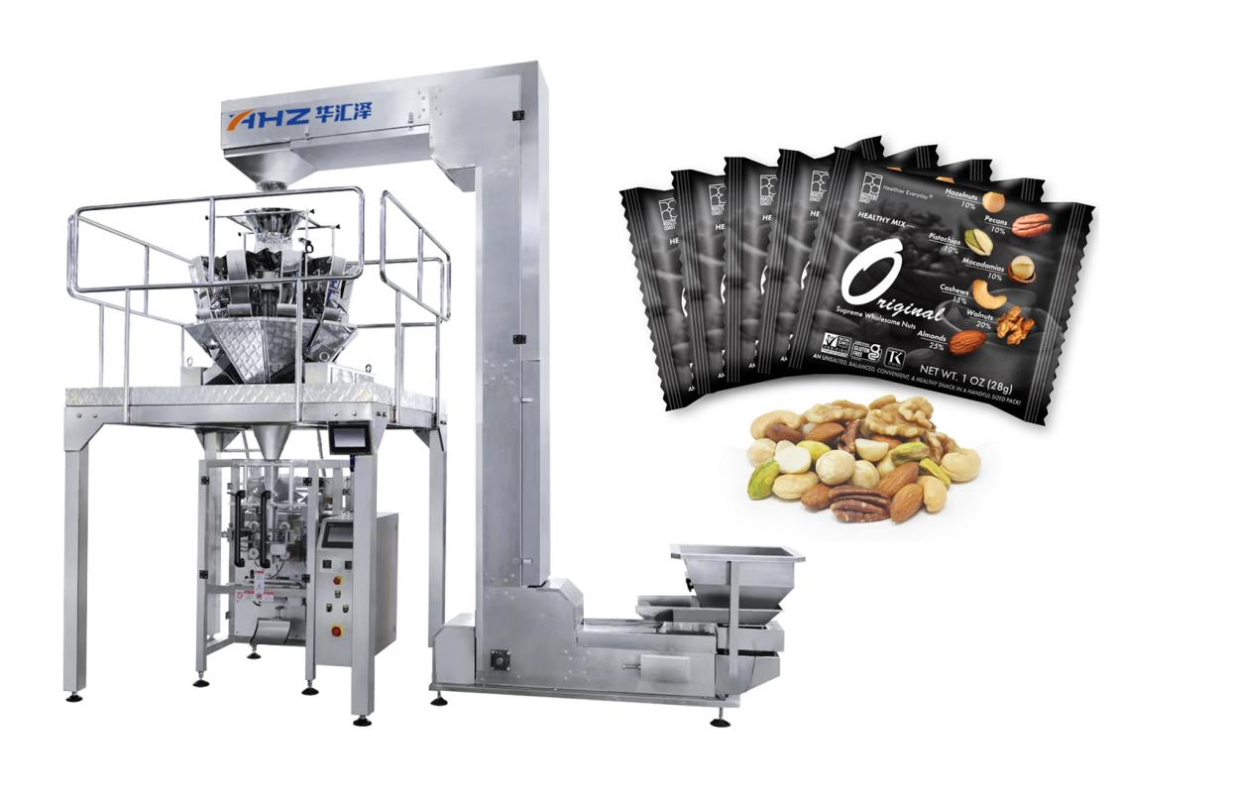
Equipment features:
1. High-precision structure, easy operation and maintenance.
2. PLC touch screen, stepper motor control, convenient and accurate bag length setting.
3. Frequency conversion speed regulation, simple, fast, time-saving and film-saving.
4. From filling, weighing, bag making, sealing, date printing, all done at one time.
5.Many bag shapes available – tell us what you need.
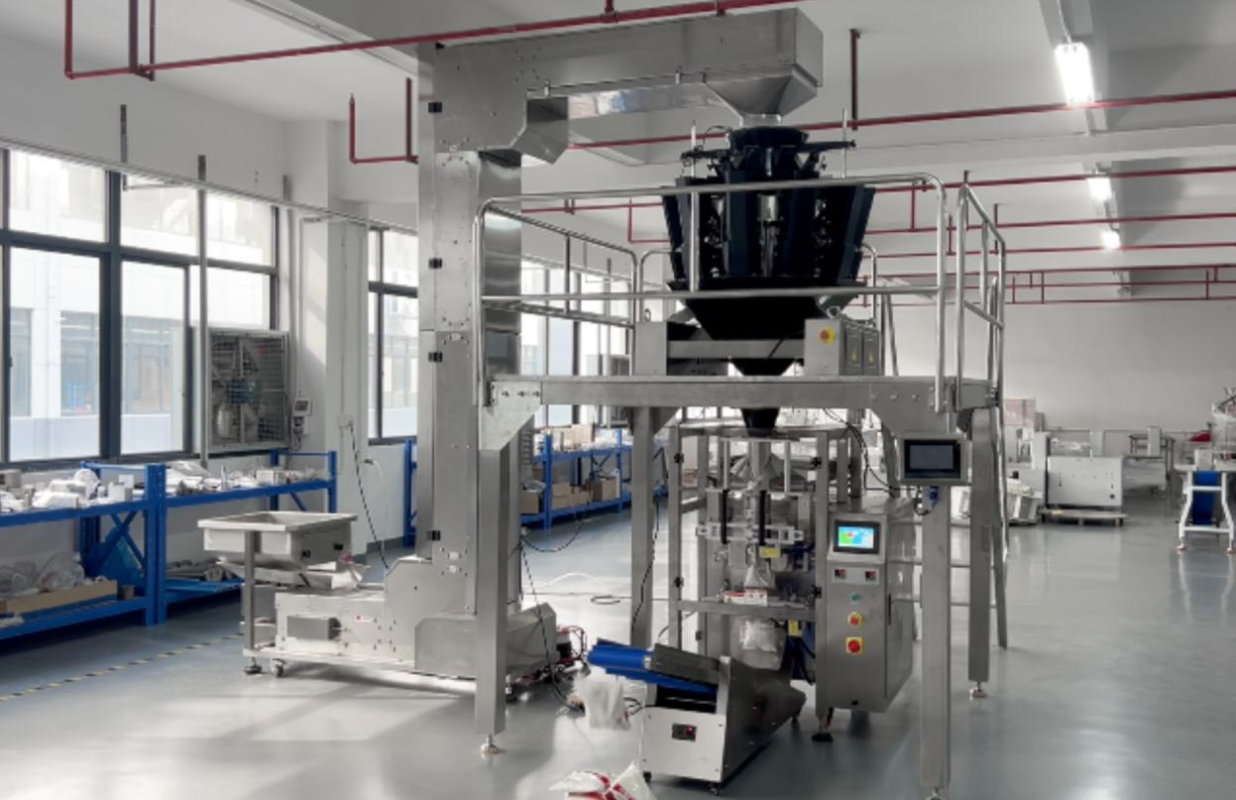
Causes and solutions of common faults of vertical packaging machine
The following are some common problems and their solutions:
1.Inaccurate positioning
- Cause: loose or damaged transmission chain.
- Solution: Check the tightness and wear of the transmission chain regularly, and replace damaged parts in time.
2.Improper temperature control
- Cause: unstable power supply voltage, poor wire connection, aging of electrical components, etc.
- Solution: Verify the stability of the power supply voltage,verify proper wire connections, and replace aging electrical components in time.
3. Electrical failure
- Cause: unstable power supply voltage, poor wire connection, aging of electrical components, etc.
- Solution: Check whether the power supply voltage is stable, ensure that the wires are well connected, and replace aging electrical components in time.
4. Sensor failure
- Cause: improper sensitivity setting, damaged sensor or loose connection line.
- Solution: Optimize sensor sensitivity according to product characteristics and packaging requirements, check and repair or replace damaged sensors, and ensure that the connection line is firm.
5. Electrical system failure
- Cause: circuit breaker problem, relay failure, unstable power supply.
- Solution: Check the circuit breaker status, use a multi-meters to detect the relay status, and ensure stable power supply.
6. Abnormal mechanical structure
- Cause: loose transmission belt, worn bearings, loose or falling mechanical parts.
- Solution: Check the tightness of the transmission belt, adjust or replace if necessary; then check the condition of the bearings, and replace damaged bearings in time; finally thoroughly check all mechanical parts to ensure that there is no looseness or falling off, and repair or replace if necessary.
7. The heat sealer body fails to heat up
- Reason: The packaging machine circuit is faulty, the heating tube is faulty, and the fuse is damaged.
- Solution: Check the packaging machine circuit, find the fault and repair it;then directly replace the heating tube; at last replace the fuse in time.
8. Heat sealer can’t control temperature
- Reason: The temperature regulator isn’t working, and the thermocouple has a short circuit.
- Solution: Replace the temperature regulator; and change the thermocouple.
9. The paper supply motor cannot operate normally
- Reason: The paper supply control lever is stuck, the starting capacitor is faulty, the power board or the fuse is faulty, and the paper supply proximity switch is faulty.
- Solution: Fix the jammed paper feed control lever; and replace the starting capacitor; also repair the power board circuit, replace the fuse; finally replace the paper supply proximity switch.
10. Bag pulling motor failure
- Cause: control board failure, circuit failure, stepper motor driver failure, bag pulling proximity switch damage or bag pulling signal cams too far apart.
- Solution: Replace the control board and check and repair the packaging machine circuit; then change the stepper motor driver; replace the bag pulling proximity switch or shorten the distance between the bag pulling signal cams.
11. Packaging materials are easily broken during operation
- Cause: paper supply proximity switch failure, irregular or rough packaging materials, motor circuit failure at the paper supply position.
- Solution: Replace the paper supply proximity switch; and trim unqualified packaging materials;finally check and repair the paper supply motor circuit.
12. Liquid packaging machine unloading is unstable
- Cause: wrong installation of the plug position, blockage of the pipeline, loose position of the plug rocker.
- Solution: First Correctly adjust the plug position; also dredge the pipeline; finally tighten the screws around the plug rocker.
13. The seal is not tight
- Cause: low sealing temperature, uneven material distribution or quality problems of the material itself.
- Solution: best to Increase the heat sealing temperature appropriately; and improve the uniformity of material distribution; at best choose better quality packaging materials.
But most (Vertical packaging machine for liquids,Vertical packaging machine for powders, Vertical packaging machine for granules) packaging machines for puffed food can be solved by regular inspection, maintenance and timely replacement of damaged parts. For complex faults, it is recommended to contact professional maintenance personnel or equipment manufacturers for diagnosis and repair.
We have a professional after-sales team. From installation, commissioning to any problems in the later use process, we can respond quickly, provide technical support and maintenance services, and can also customize according to your needs.